The lost wax process is a ritual of transformation—where fleeting forms are given permanence, and imagination is cast into legacy.
A two mold process.
-
ORIGINAL SCULPTURE
The Process begins with an original artwork, typically sculpted in clay or another malleable material. This model captures every detail the artist intends to preserve in bronze. This original master piece is the foundation for all that follows.
-
THE 1st MOLD
A flexible rubber mold is made around the original sculpture, supported by a plaster mother mold that helps the rubber keeps its shape. This mold holds an exact negative impression of the original sculpture. It allows for multiple wax copies to be produced.
-
WAX CASTING & CHASING
Using the 1st mold, hot liquid wax is poured in several layers. Each coat is carefully timed, allowing it to cool slightly before the next is added, ensuring the surface is covered evenly and consistently. This creates a durable wax form, rich in surface detail, ready for the next phase of casting. The wax pattern with then be chased, this is where seam lines will smoothed and the wax pattern will be carefully inspected and worked to be sure that all of the detail from the original master piece is intact.
-
SPRUING & GATING
Once the wax pattern is worked rods, called “spurs,” are attached to the wax sculpture to form channels for the bronze to flow through, this is called a “gate” and air and gas to be released, these are called “vents”.
-
THE 2nd MOLD - INVESTMENT MOLD
The investment mold will serve as the final form for the bronze casting, built to withstand the intense heat of the molten bronze. Each wax pattern is repeatedly dipped into a liquid ceramic slurry and coated with layers of fine sand in varying grits. These layers are allowed to fully dry and cure between coats, gradually forming a durable ceramic shell. Once complete the mold is ready for the bronze pour.
-
BRONZE POURING
Once the investment mold is complete it will be placed into a furnace that burns out the wax, leaving a hot hollow cavity in its place, this is the “lost wax” stage. The empty shell is placed into a warm bed of sand where a crucible with molten bronze over 2000°F will fill each mold. As the bronze fills the mold it will take the exact shape of the original wax pattern, capturing every fine detail.
-
METAL CHASING
Once cast, the sculpture goes through a process called metal chasing, where it is cleaned and refined by hand. The ceramic shell, sprues, and gates are removed, and any separate sections of the sculpture are carefully welded together. Each weld is then ground down and meticulously retextured using a variety of tools to seamlessly math the artists original detail and vision
-
PATINA
Using heat and chemicals, a patina is applied to the surface of the bronze. This final coloring process enhances textures, adds richness, and protects the metal. Every patina is unique, adding a final layer of artistry to the sculpture.
-
The Unveiling
With fire behind it and time etched within, the final bronze sculpture emerges-freed from its shell, forged in metal and faithful to the artist’s hand. What began as an idea now stands solid and enteral, ready to be seen, touched and admired. This is where the process becomes presence…and vision becomes form.
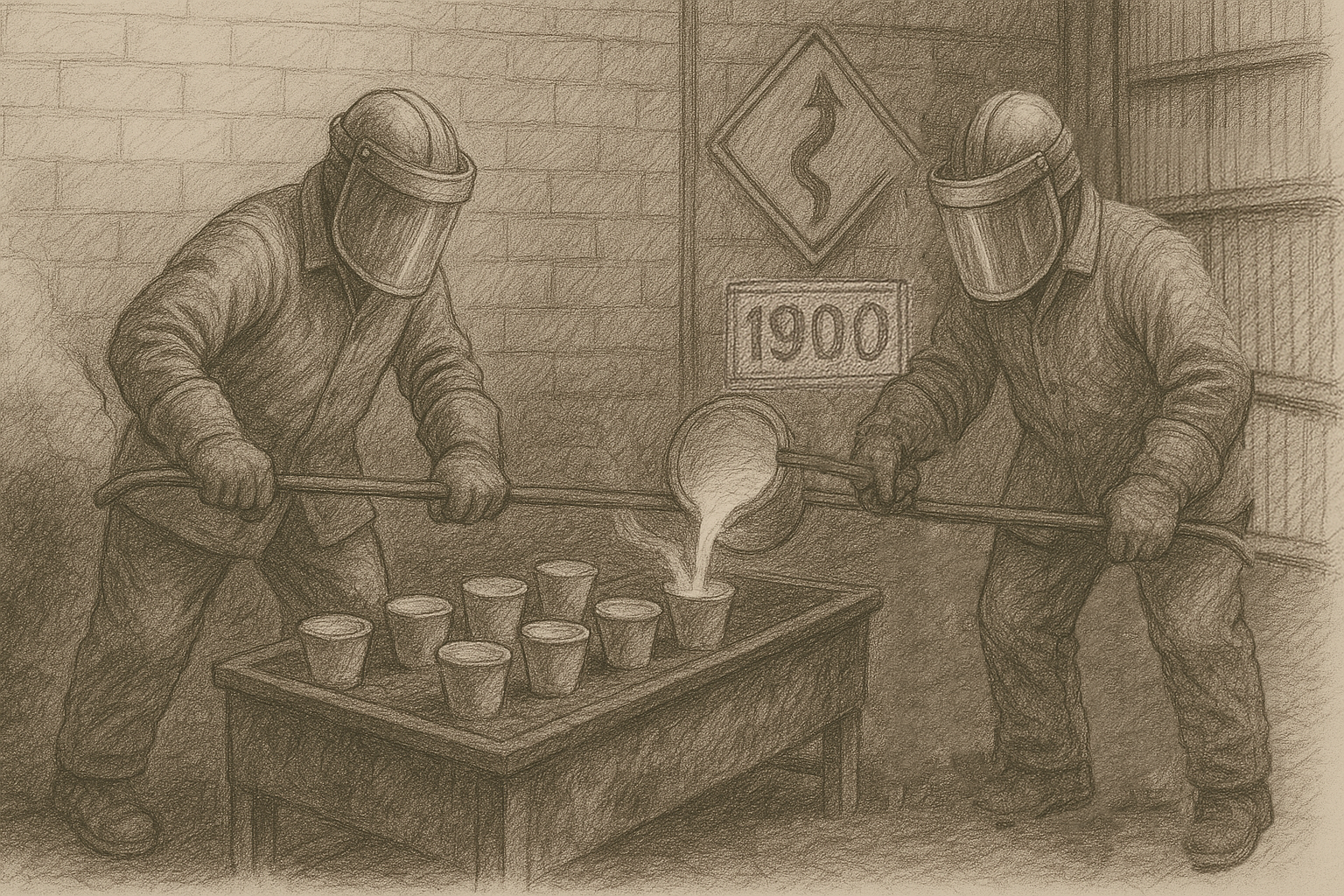